FIRST Robotics (FRC)
I joined Iron Claw 972, my school’s robotics team, in 10th grade, not realizing how significantly it would shape my passion for engineering. Robotics has equipped me with valuable technical skills, including Finite Element Analysis (FEA), mechanical design, CAD modeling, precision machining, electrical assembly, applied physics, and functional prototyping. Additionally, it has developed my proactive approach, leadership capabilities, and teaching abilities.
Charged Up – 2023
In my first season (2023), my team won the San Francisco Regional as part of the first-seeded alliance among 50 teams, and subsequently won the Archimedes division at the World Championships, ranking team 972 within the top 70 out of over 3,500 active teams. This season significantly broadened my skillset, including CNC machining, mechanical desing, assembly and electrical systems. While my direct contributions to the competition robot were limited, this experience sparked my passion for robotics, collaborative engineering, and teamwork.
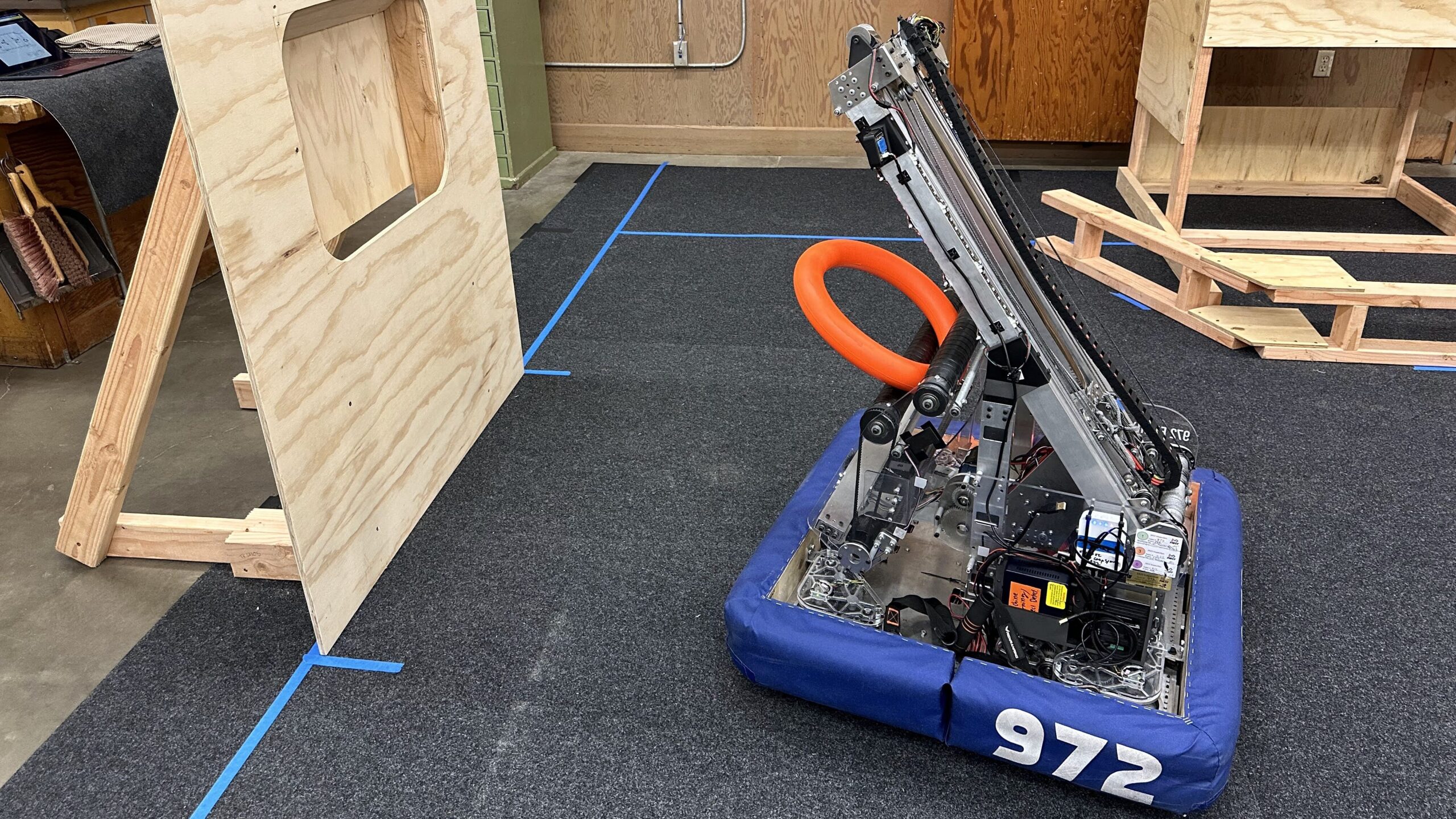
Crescendo – 2024
Starting in the 2024 offseason, I led manufacturing training sessions for new students, teaching the operation of mills, lathes, bandsaws, and drill presses. During the build season, I directed both the machining team and a prototyping group. The 2024 FRC game involved shooting foam rings into scoring zones and climbing a chain.
Initially, we prototyped over-the-bumper intakes featuring polycarbonate rollers pivoting from within the frame onto the robot’s bumpers, alongside two shooter designs. The main challenge proved to be indexing and centering game pieces. Passive wedge-based funneling was insufficient, leading to my conclusion that active wheel-based funneling was necessary.
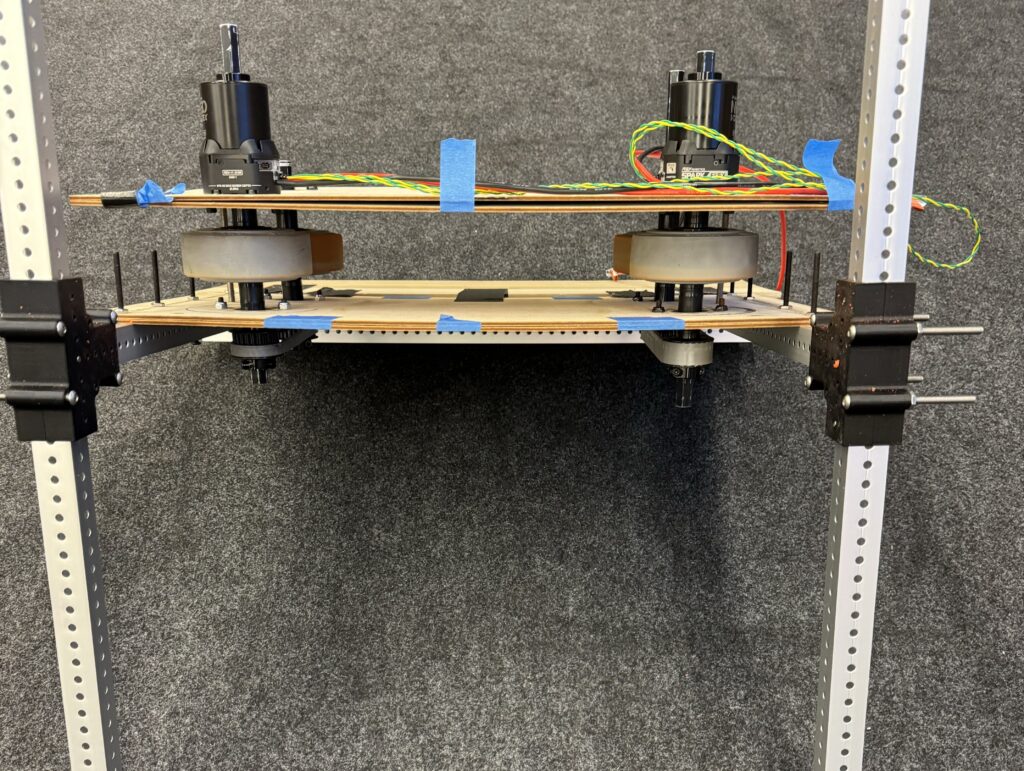
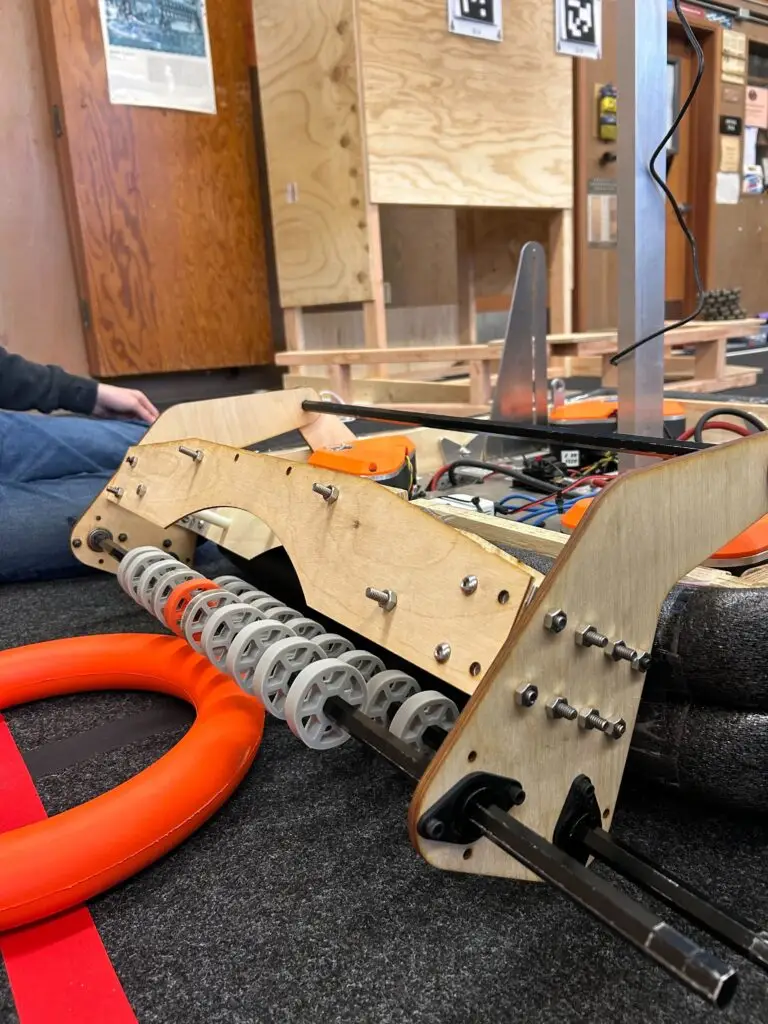
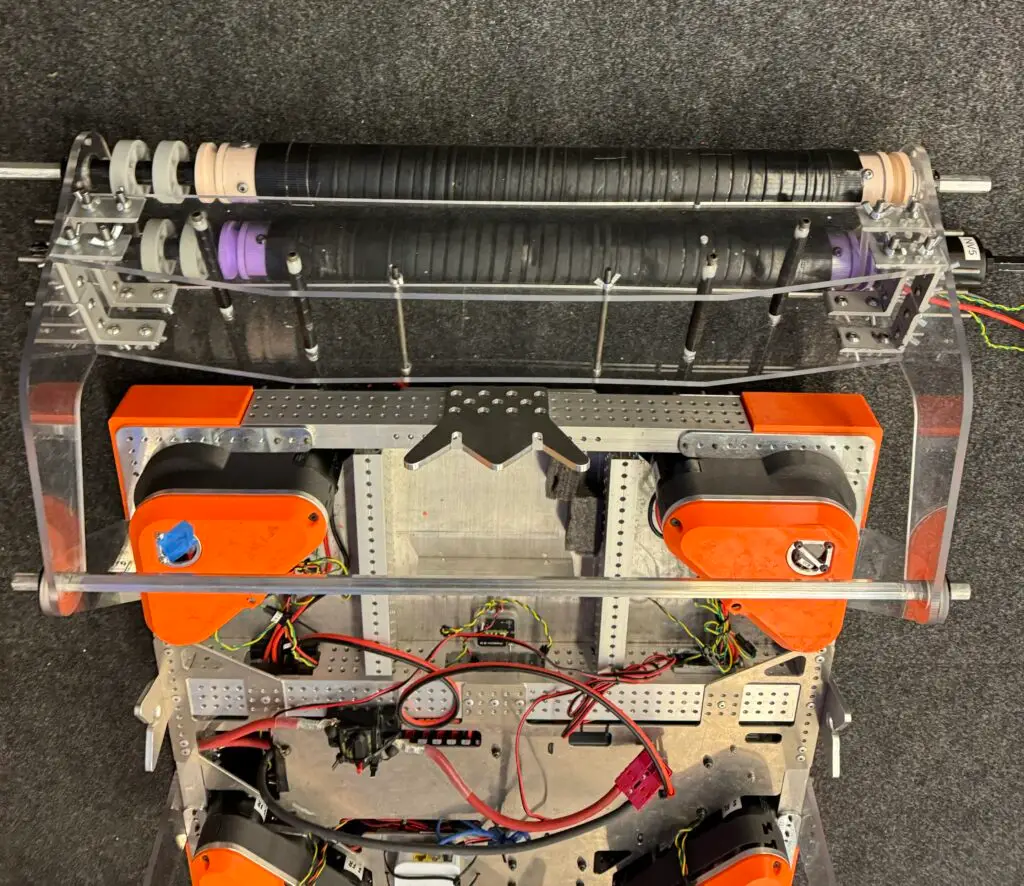
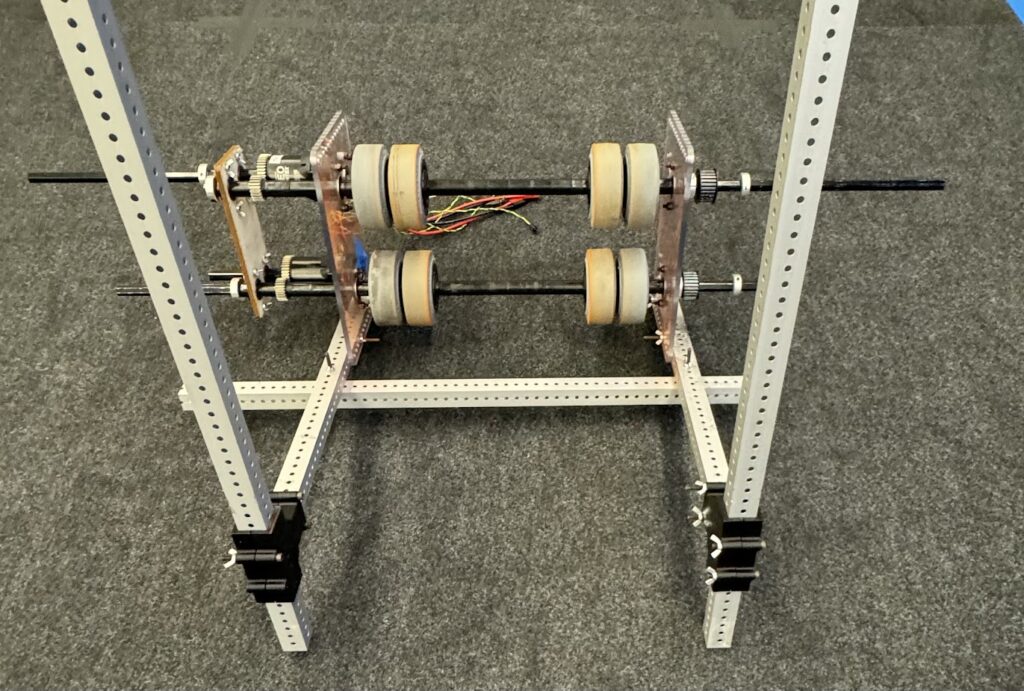
One shooter prototype, inspired by FRC Team 95, utilized four sets of wheels—two on each side and two vertically aligned. The second prototype, inspired by baseball pitching machines, had two side-mounted wheels. Testing showed the 95-styleshooter provided better accuracy and power by effectively transferring velocity forward rather than inducing spin. Additionally driving each side of the wheels of the 95 shooter at differential speeds created a gyroscopic effect, resulting in more consistent trajectories.
The final intake design evolved into an under-the-bumper (UTB) style. This approach simplified design complexity by removing the need for pivot mechanisms and provided more substantial protection against impacts.
Parallel to prototyping, I led the machining of our drivetrain, comprising four 2”x1” rails with a standard #9 hole pattern, one central 2”x2” rail, a 1/4” 6061 aluminum belly pan for a low center of gravity, and a 1/16” 6061 electrical panel (“brainpan”) designed for easy component access. We employed SDS Mk4i swerve modules and fabricated a protective 1/16” polycarbonate cover plate. More infomation about this can be found at FRC Design who featured 972’s standard drive base on their FRC design course.
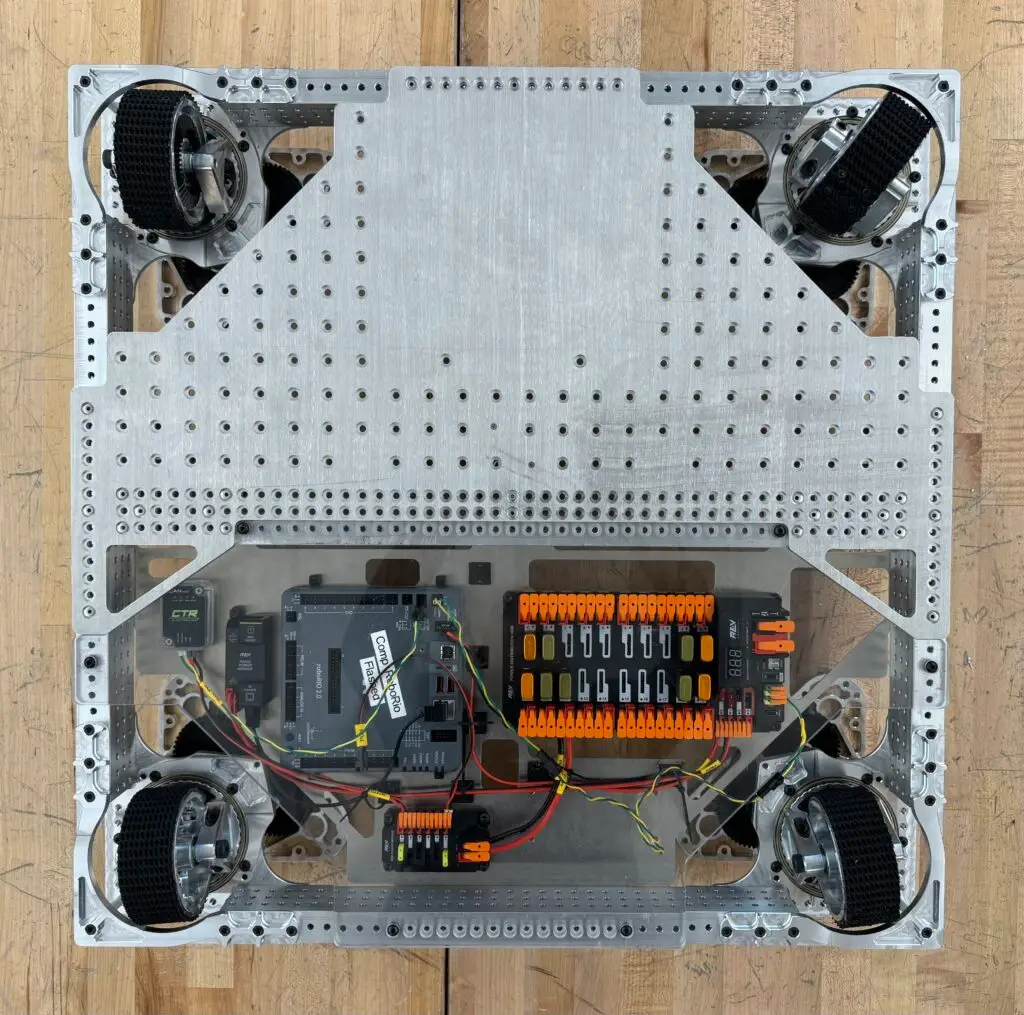
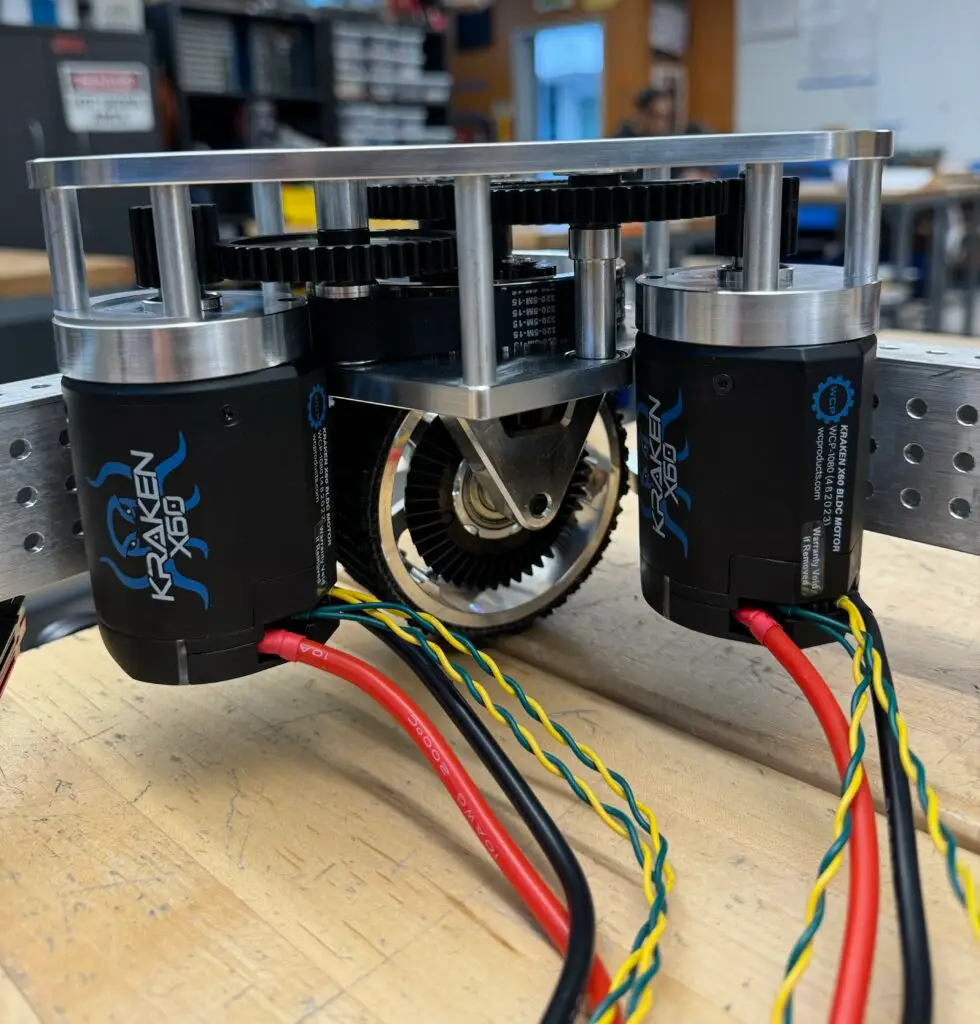
Under my experimentation, machining efficiency improved drastically, reducing runtime from over five hours to just 35 minutes. This was achieved by integrating Fogbuster mist lubrication, optimizing machining strategies, and refining feed rates and speeds. I found that there is a minimal difference between 2D Adaptive and 2D Pocket operations for weight reduction pockets, so using 2D pocket increased MRR while also reducing toolpath genoration times (which could take up to 5 minutes with 400+ pockets and 2D Adaptive). Our Tormach 24R router operated effectively at 100 ipm, 24,000 rpm, full axial depth, and 0.1” radial cuts. Comprehensive CAD design reviews on Onshape also drove final subsystem fabrication.
Our design methodology was guided by clear functional requirements, driving master sketches and detailed block CAD models, which informed subsystem development and overall robot architecture.
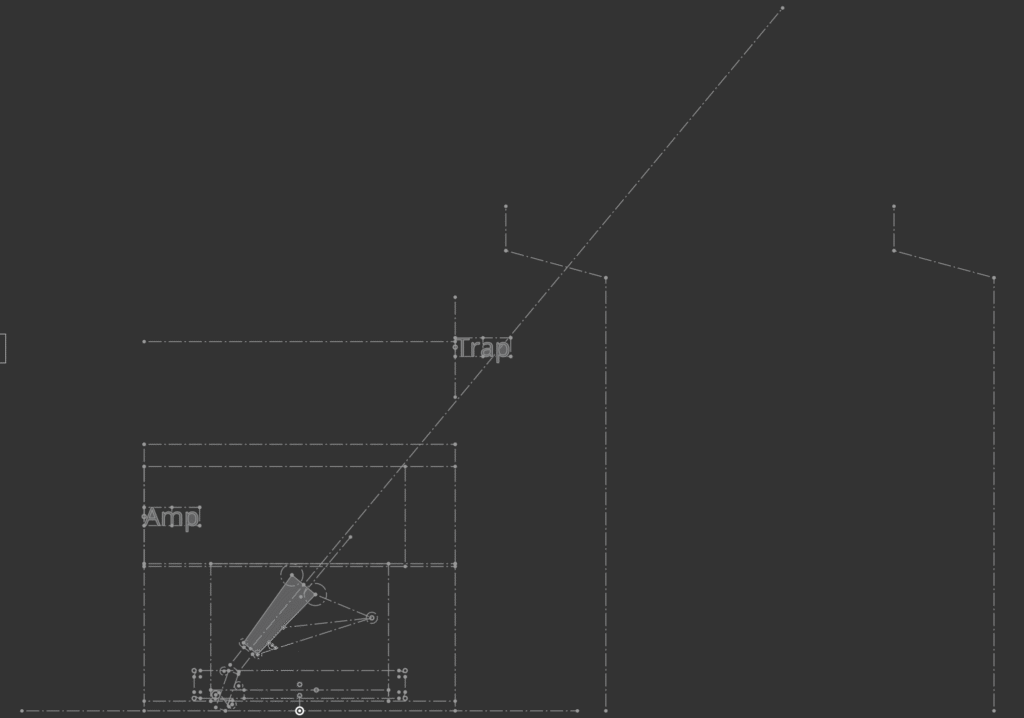
Our final robot design drew significant inspiration from Team 3467 – Windham Windup. The configuration included a pivot-mounted, 95-style shooter with independently driven wheel sides. This was mounted on an arm powered by four Kraken x60 motors across two gearboxes. The robust gearing ensured arm stability and prevented backdrive during the end of matches where electrical power was cut to robots.
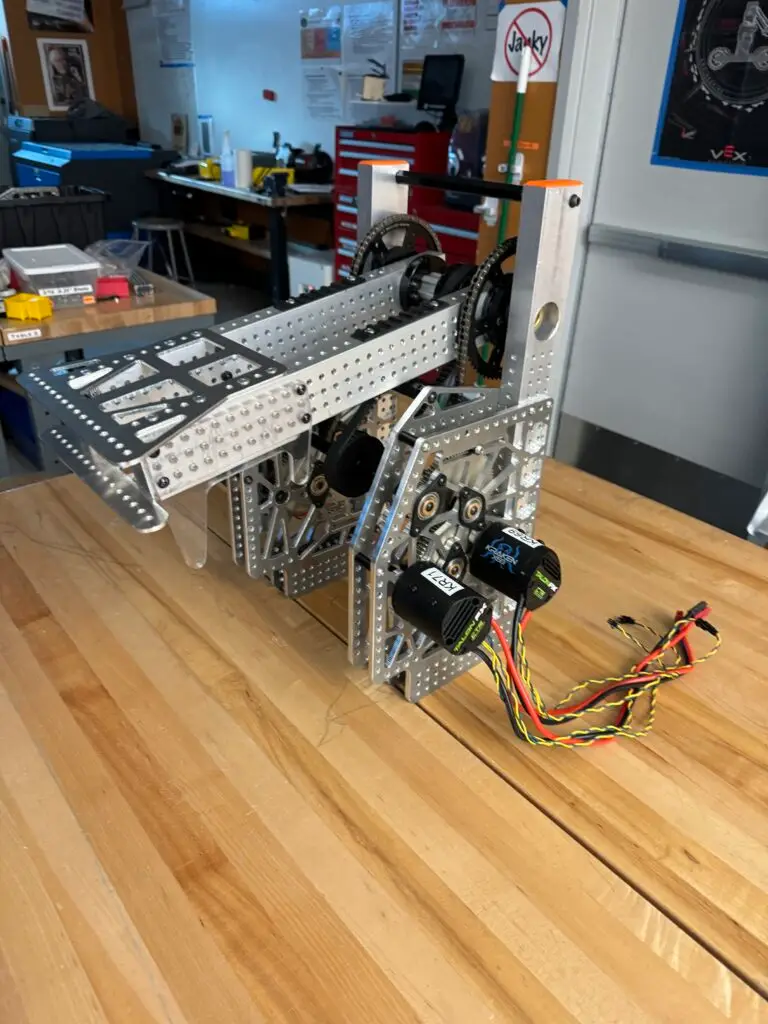
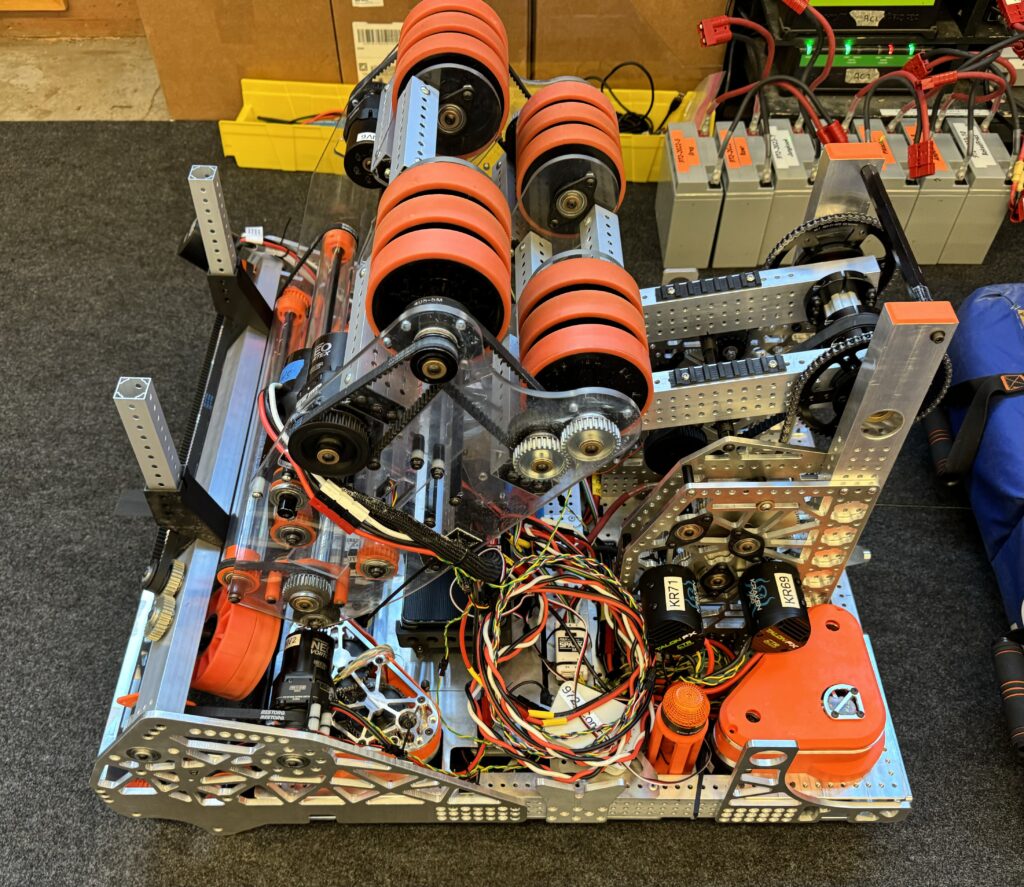
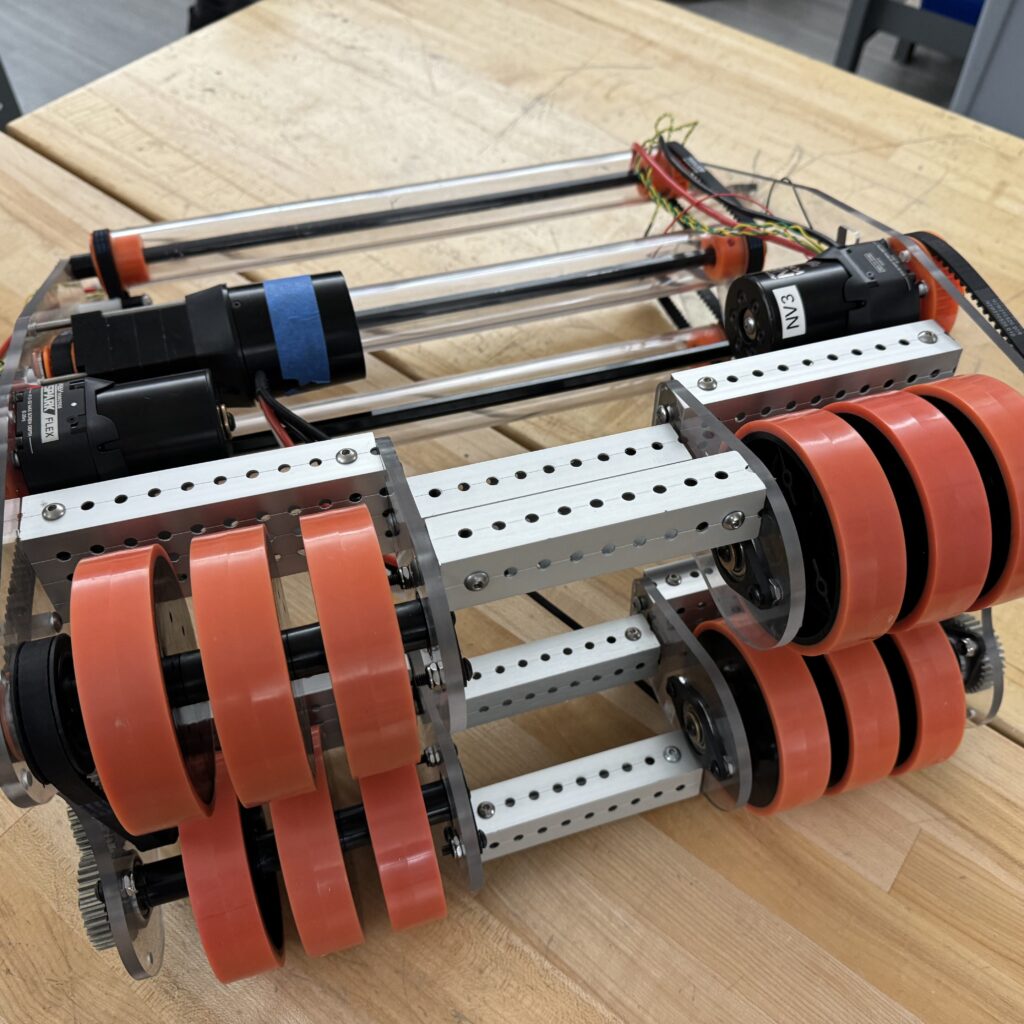
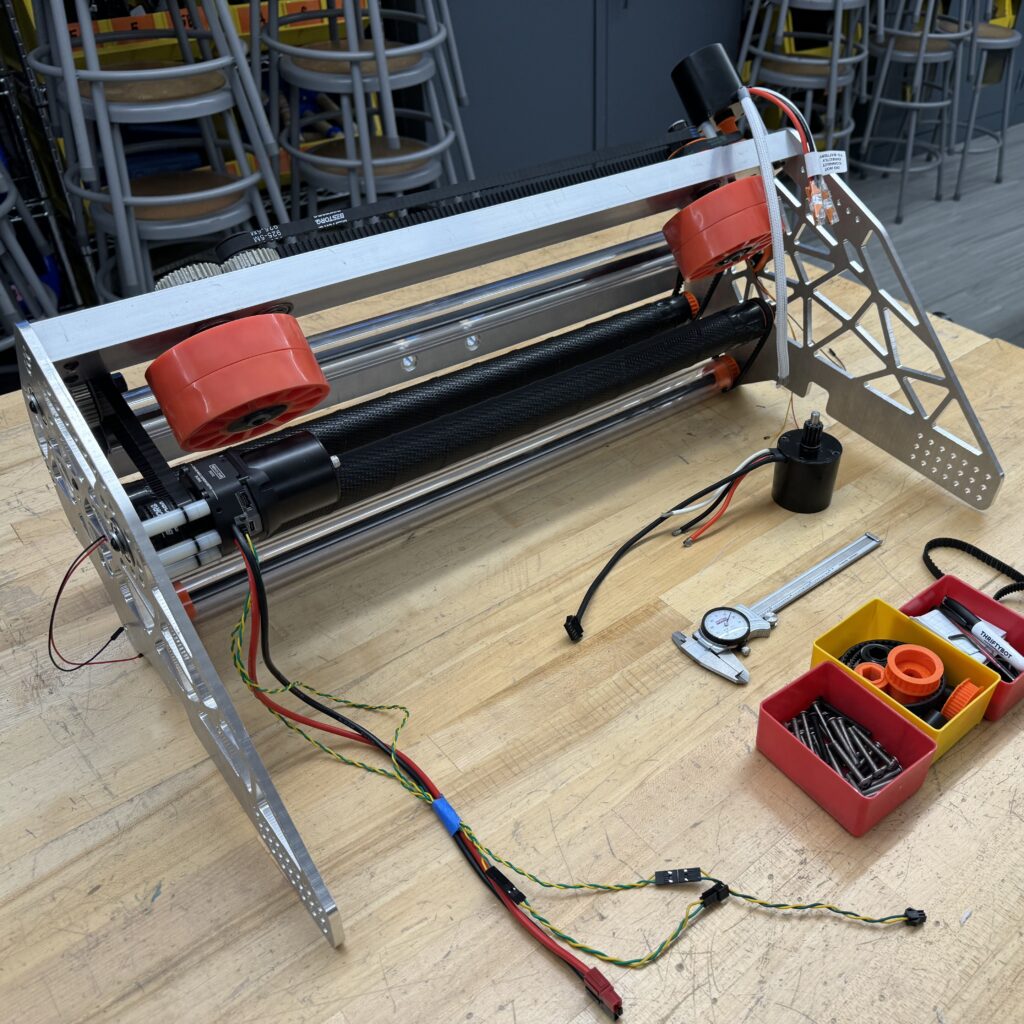
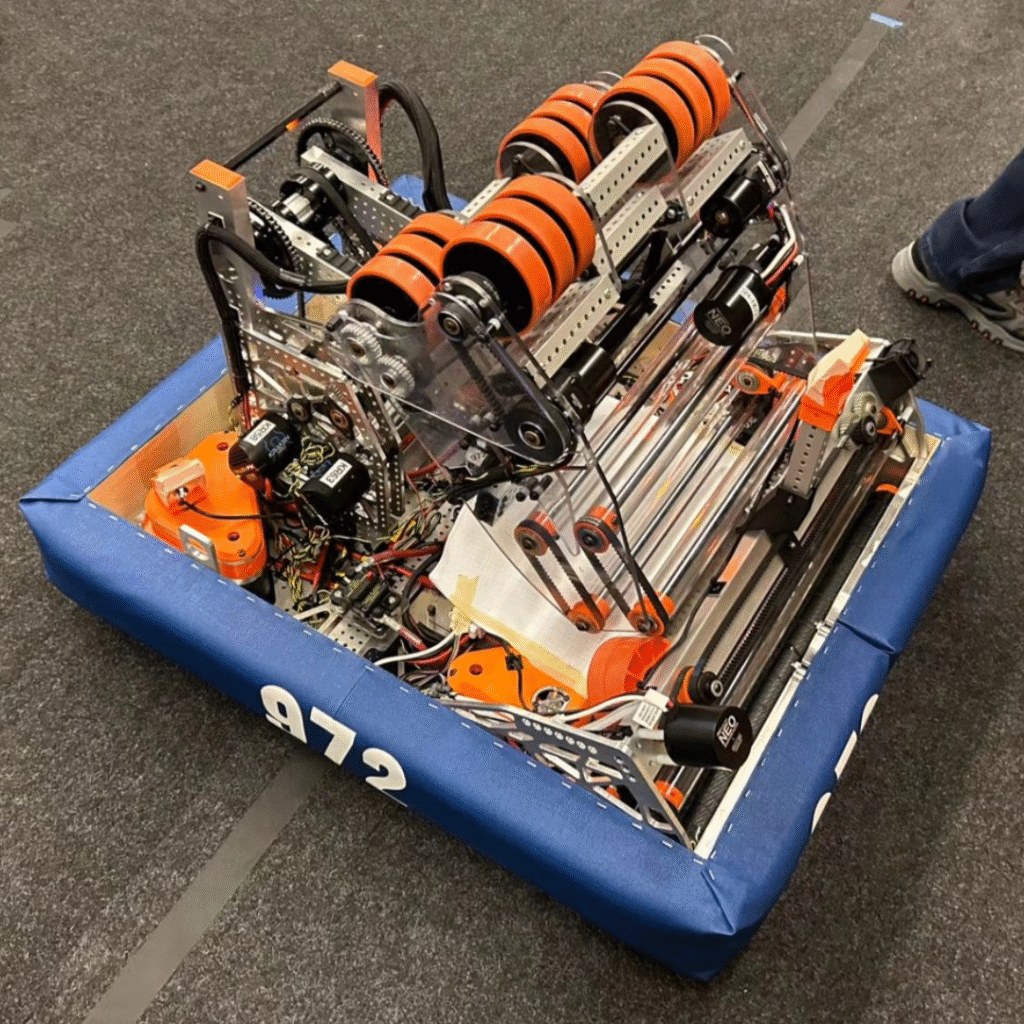
During our first competition, three issues emerged:
- Chain failures following belt slips and arm crashes.
- Intake bar deformation upon impact.
- Arm encoder misalignment due to belt slippage.
To address the intake deformation, I conducted Finite Element Analysis (FEA) simulations in Onshape, modeling worst-case collision scenarios with forces of up to 7700N. Reinforcing the intake bar with a mild steel C-channel effectively mitigated the issue. The reinforcement was secured using 3M Scotch-Weld 2216 epoxy, cured at 200°F for 30 minutes, complemented by three alignment 10-32 bolts.
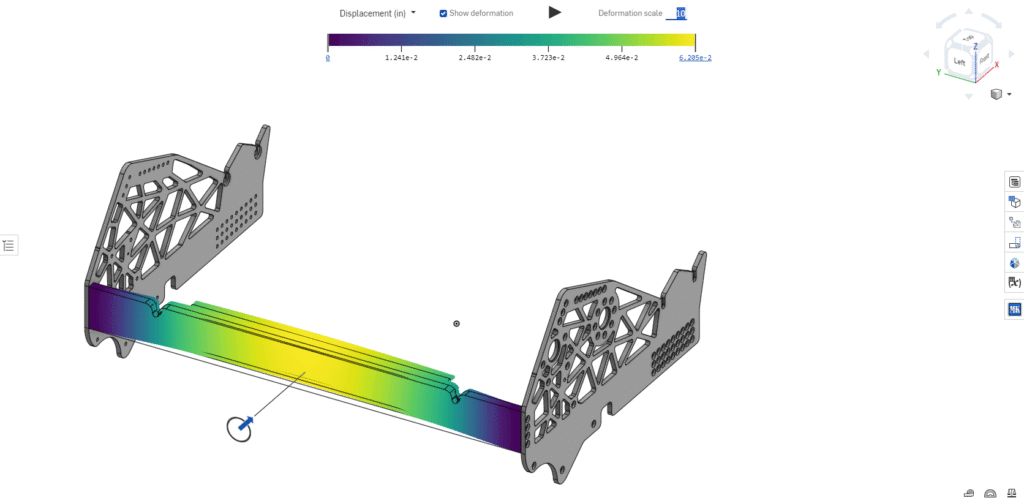
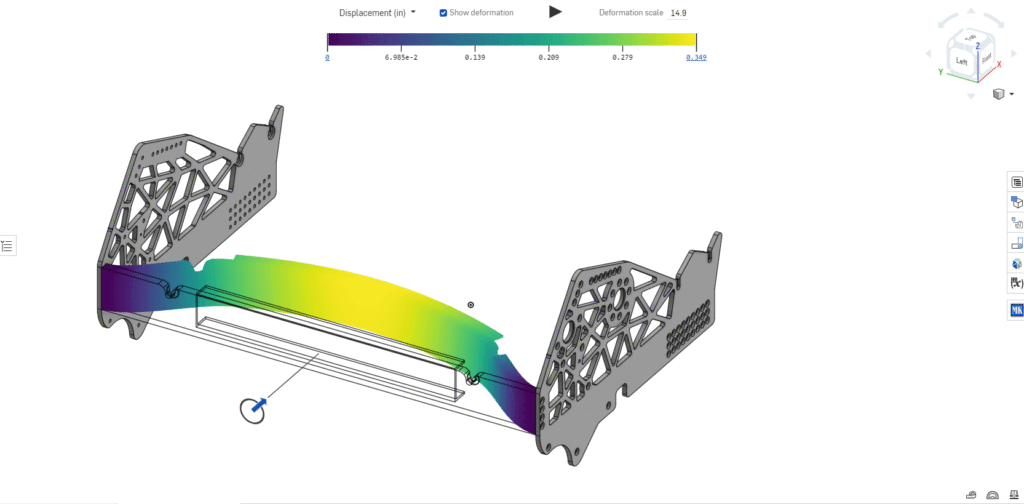
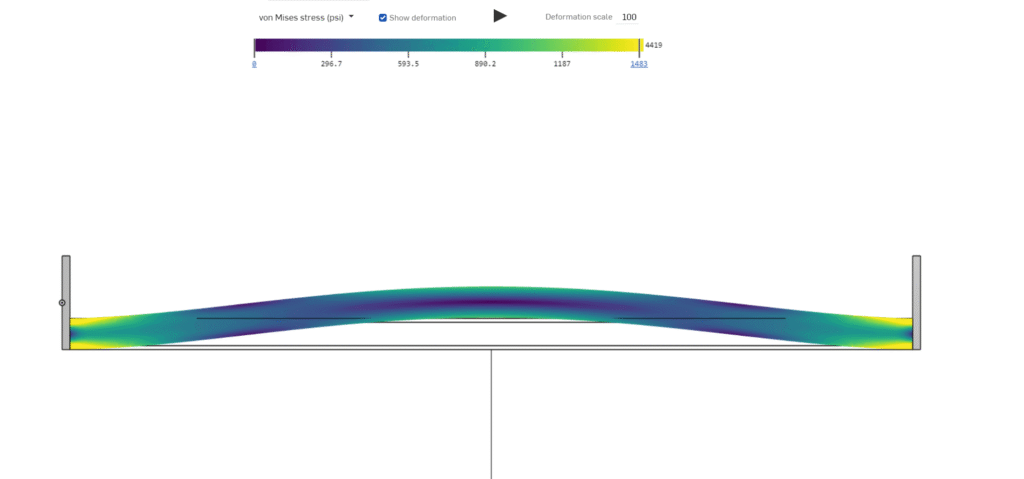
For encoder-related issues, we adopted a pragmatic approach: limiting pivot usage exclusively for climbing tasks. This solution did not hinder our competitive performance, as pivot adjustments during shooting were rarely necessary.
Although we did not qualify for Worlds, the 2024 season significantly enhanced my leadership capabilities, technical proficiency, and prepared me effectively for future engineering projects.
Reefscape – 2025
During the 2025 season, I served as Mechanical Director, leading four subteams—CAD, Electrical, Manufacturing, and Assembly—comprising 50 students. My primary objectives were to transfer critical technical knowledge, build a high-performance robot, and qualify for Einstein Field.
In the preseason, I supervised two key projects: a two-stage cascading elevator and a turret. Anticipating a pick-and-place challenge, our elevator project provided hands-on experience in design, manufacturing, and assembly. Selecting a cascading design offered advantages in reliability, rigidity, and speed compared to continuous elevators. Additionally, we integrated the elevator onto a pivot mount, adjustable via tie rods, allowing precise angle adjustments. Concurrently, I ensured the turret project reached operational readiness through targeted software revisions, giving our team valuable experience entering build season.
During the build season, I implemented three critical enhancements:
- Expanded CNC machining to significantly reduce production time and increase component accuracy.
- Developed an Alphabot—a minimal, functional robot enabling rapid autonomous routines testing and driver practice. Using our offseason elevator mounted on a standard drivetrain with a funnel intake, we identified the strategic importance of a ground intake and the necessity of automated scoring systems driven by computer vision and 3. Strategically planned robot rebuilds between competitions for continuous improvements.
- Employing our established practice of master sketches and high-fidelity CAD models, we tackled the complex intake geometry required by the 11⅞ inch-long, 4-inch PVC game pieces. Simultaneously, we optimized our drivetrain by using thinner-walled aluminum tubing, enabled by an increased weight allowance (115 lb to 125 lb), and lowering our chassis by one inch to improve stability and lower the center of gravity.
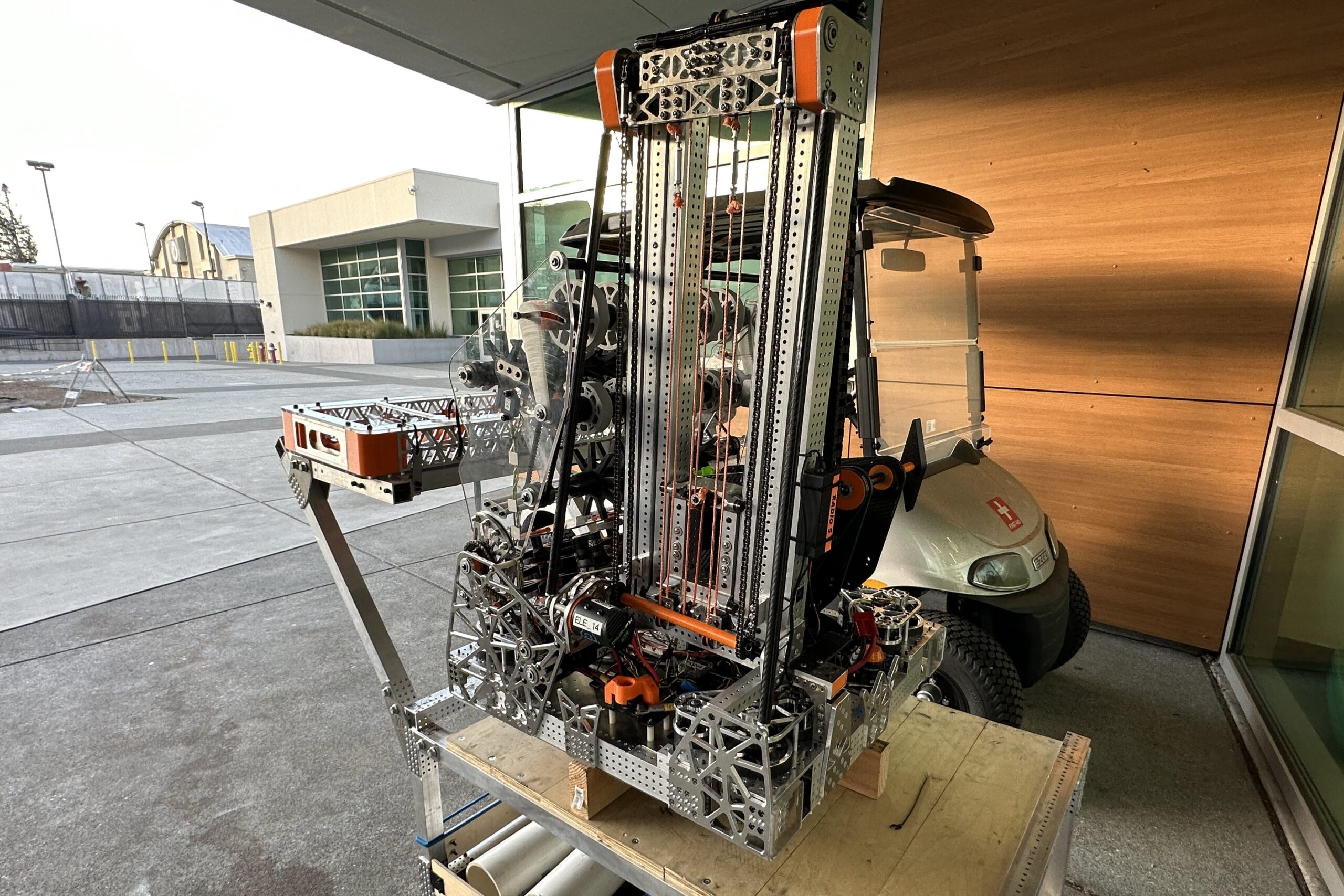
Post-first competition, we identified key performance issues and incorporated design insights inspired by Team 1678. Modifications included:
- Adding a gearbox-driven pivot on the elevator’s final stage.
- Narrowing and enhancing our intake funnel for more aggressive passive alignment.
- Completely redesigning the indexer and end-effector for effective internal gripping of game pieces.
- Weight optimization through component pocketing and motor reduction.
- Implementing advanced vision processing with dual Arducams and Orange Pi processors running Photon Vision for sub-centimeter precision localization and automated scoring.
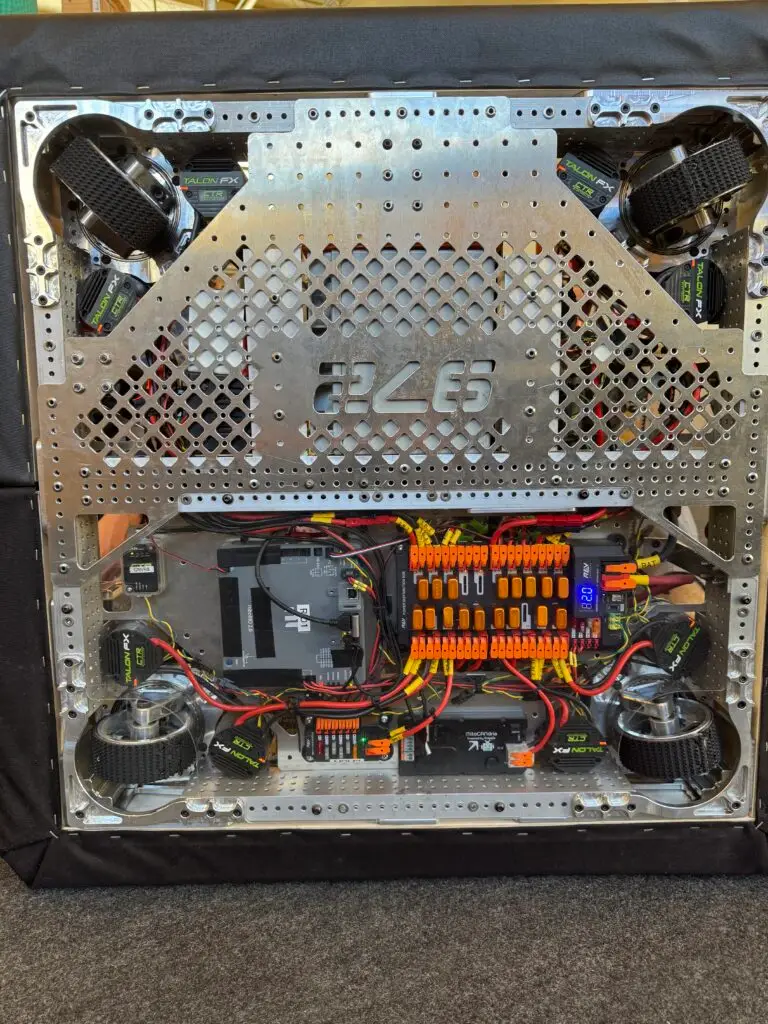
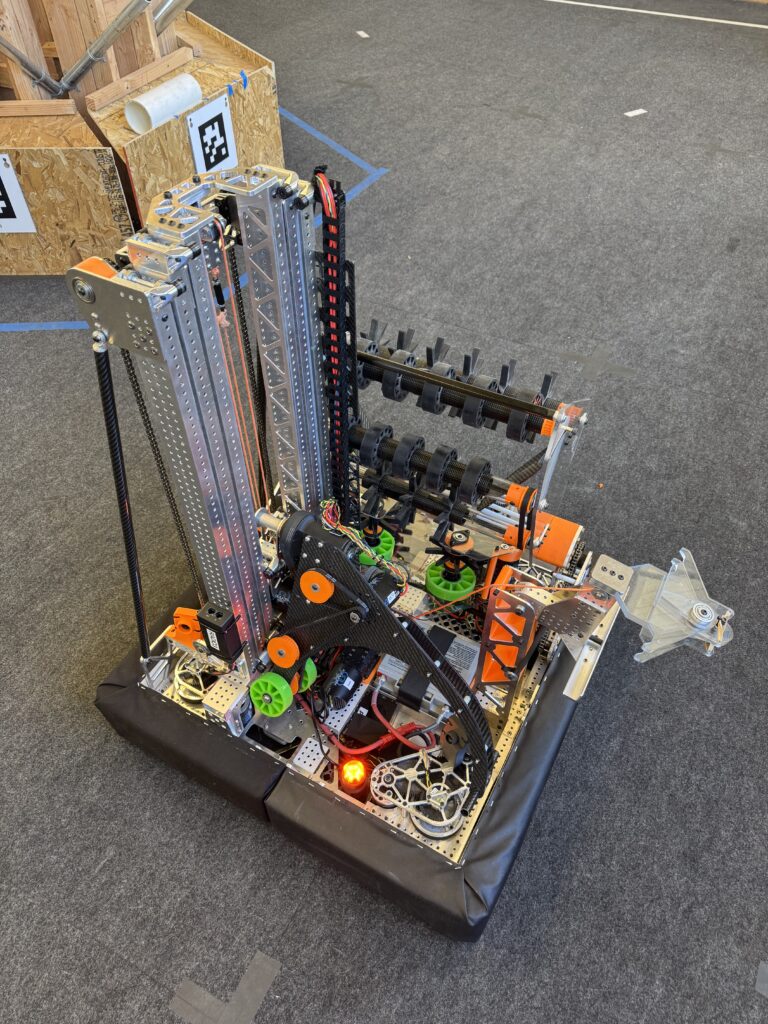
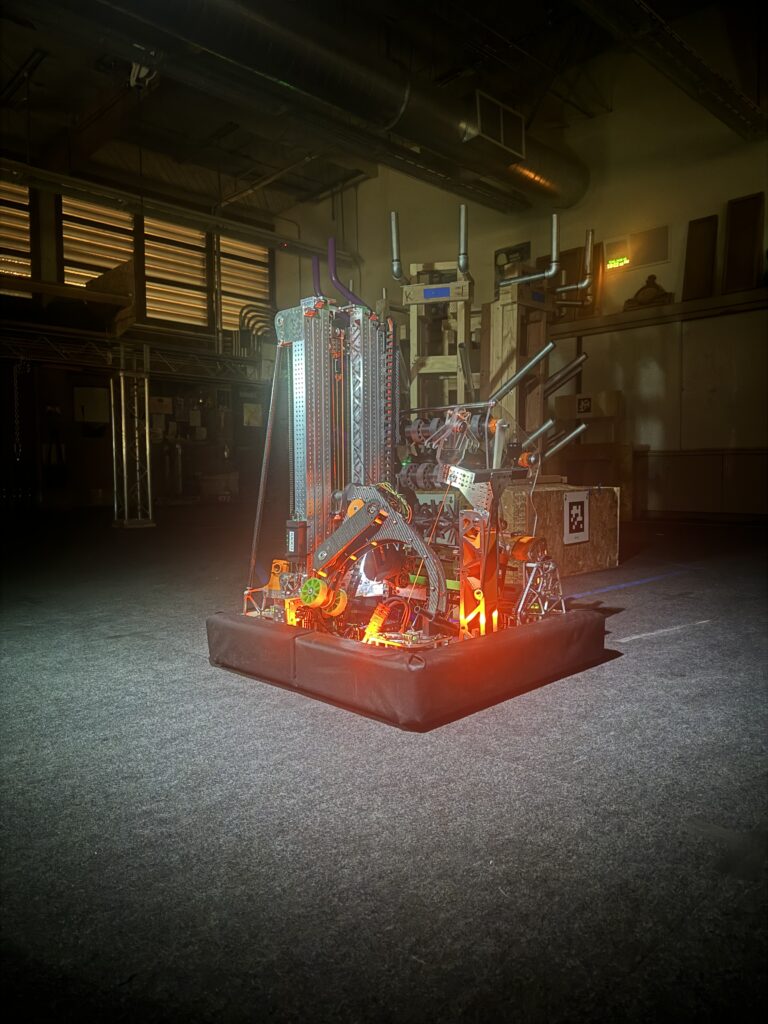
The final robot architecture featured:
- Robust climbing mechanism powered by a 60:1 gear reduction winch
- Three-stage cascading elevator driven by 1 Kraken x60
- Intake with kicker roller to accommodate all orientations of game pieces
- Belt-driven pivot gearbox packaged within the elevator carriage
- Dual-purpose end-effector utilizing bevel gear-driven grippers for PVC pipes (coral) and inflatable ball (algae)
Ultimately, Team 972 achieved finalist status at the East Bay Regional and earned the Industrial Design Award at the Sacramento Regional. Detailed documentation on our processes, machining techniques, CAD models, and methodologies is available at http://ironclaw972.org. I extend my gratitude to our mentors, students, and parents for their remarkable support and collaboration throughout these enriching three years.

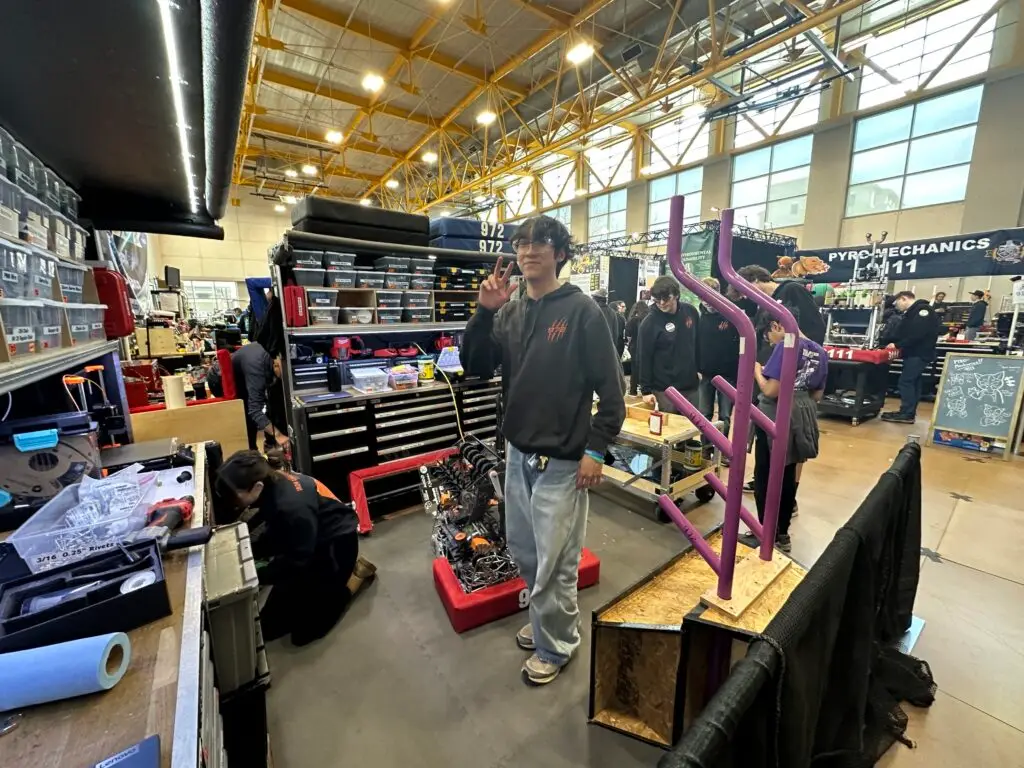
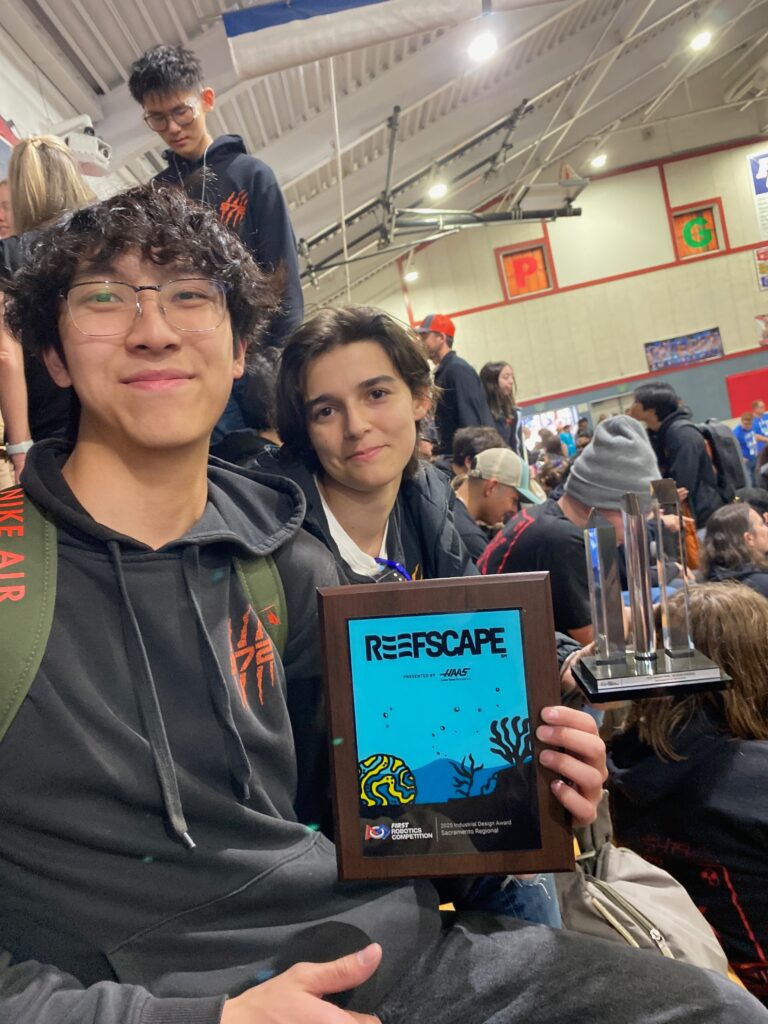
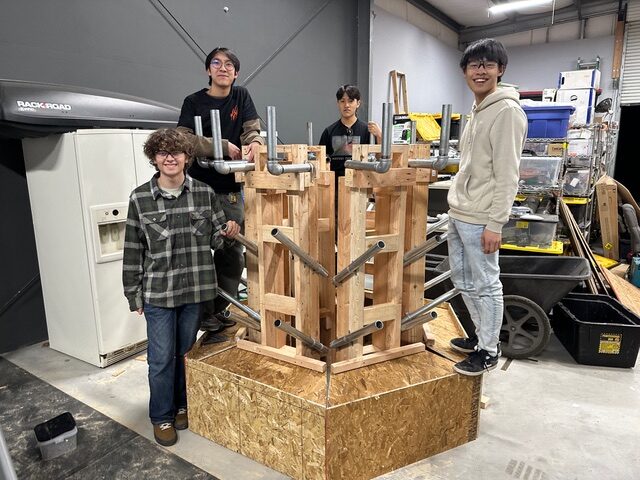
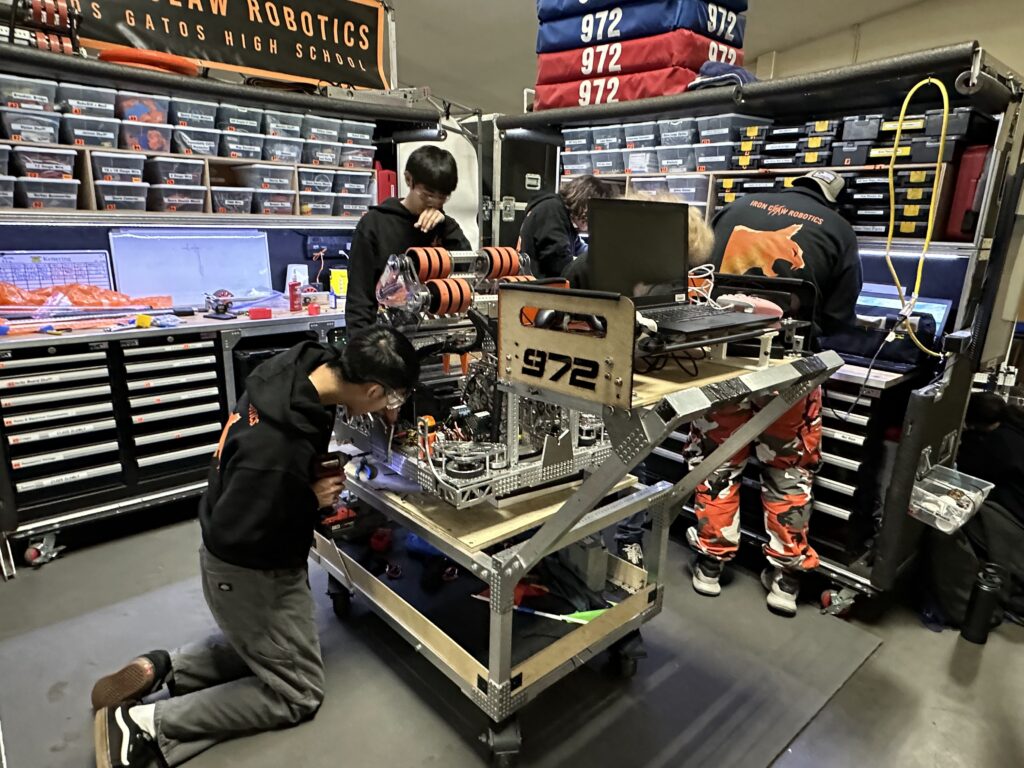