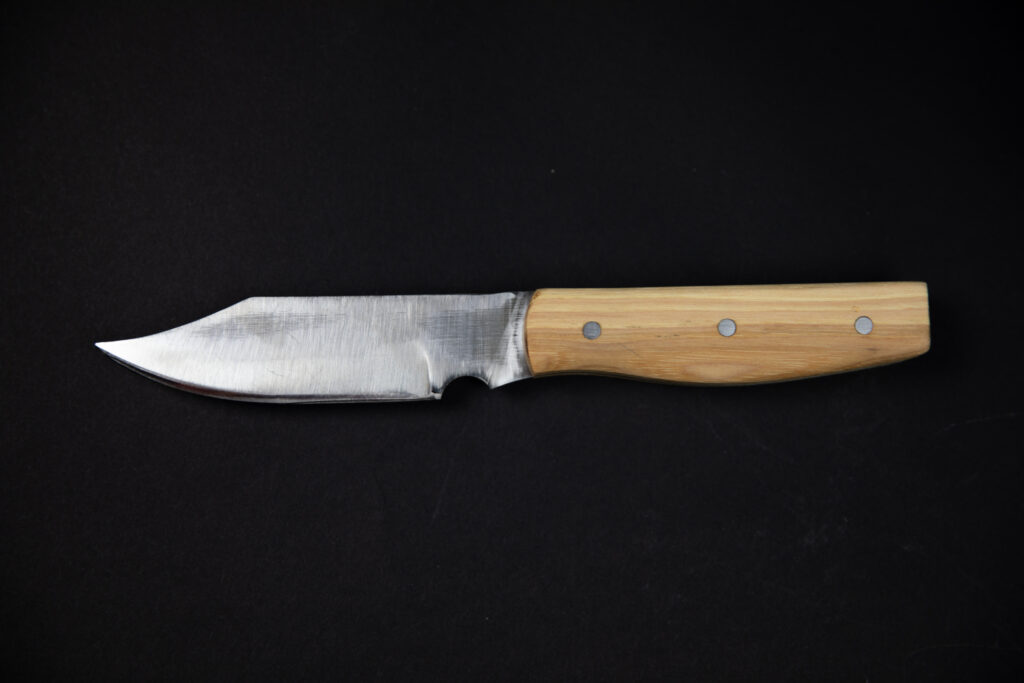
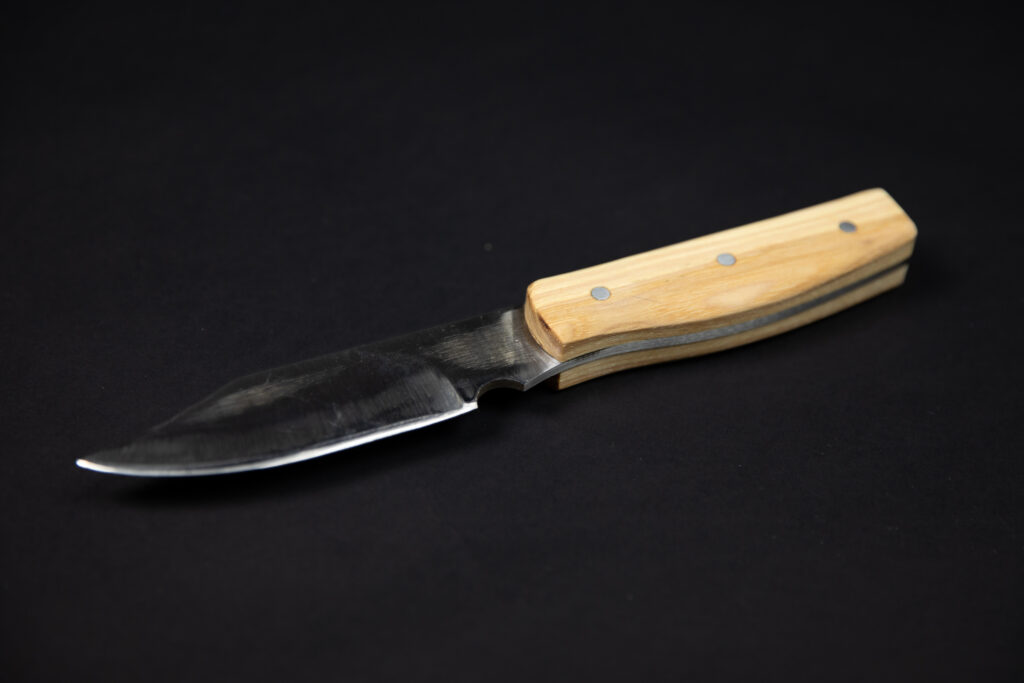
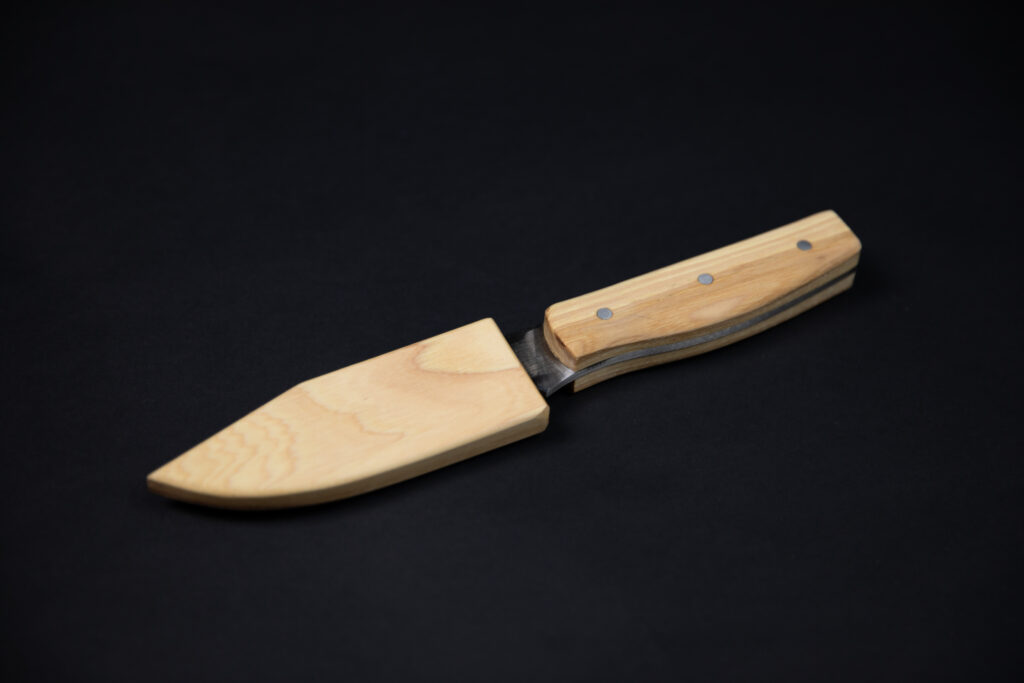
Mass Production Knife
During my third year of Manufacturing Tech at Los Gatos High School, I lead an 11-person class to design, fabricate, and assemble 16 custom knives and .
I designed a Clip-point knife with a Scandinavian grind with an integrated guard in Fusion360 which was nested to save the most amount of material and cost. The nested file was then cut out of CPM 154-CM on LGHS’s OMAX ProtoMAX water jet and handed off to 3 students to heat treat.
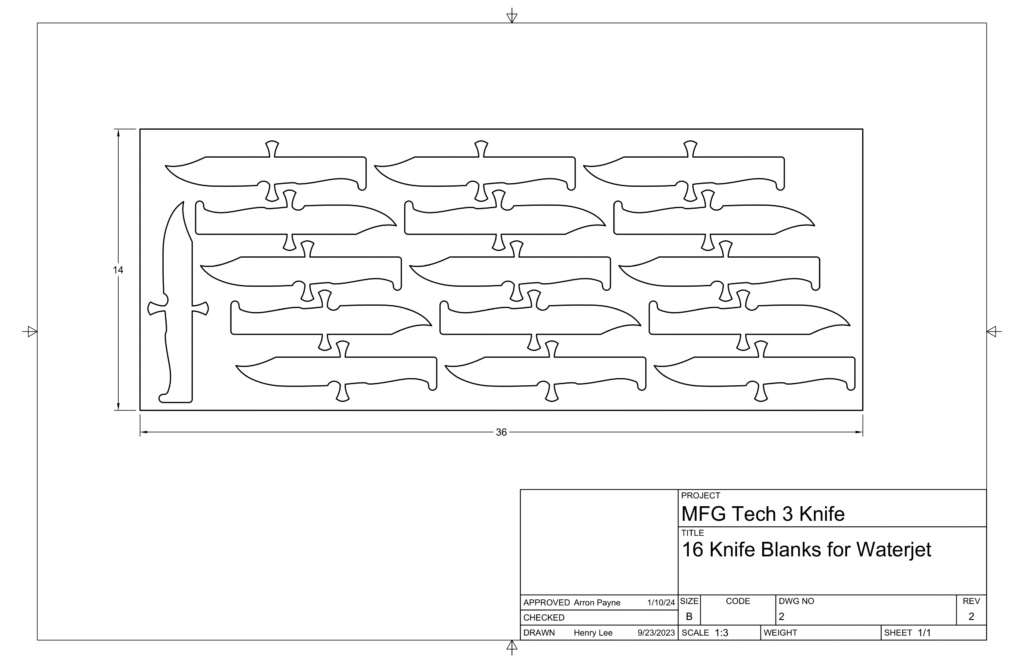
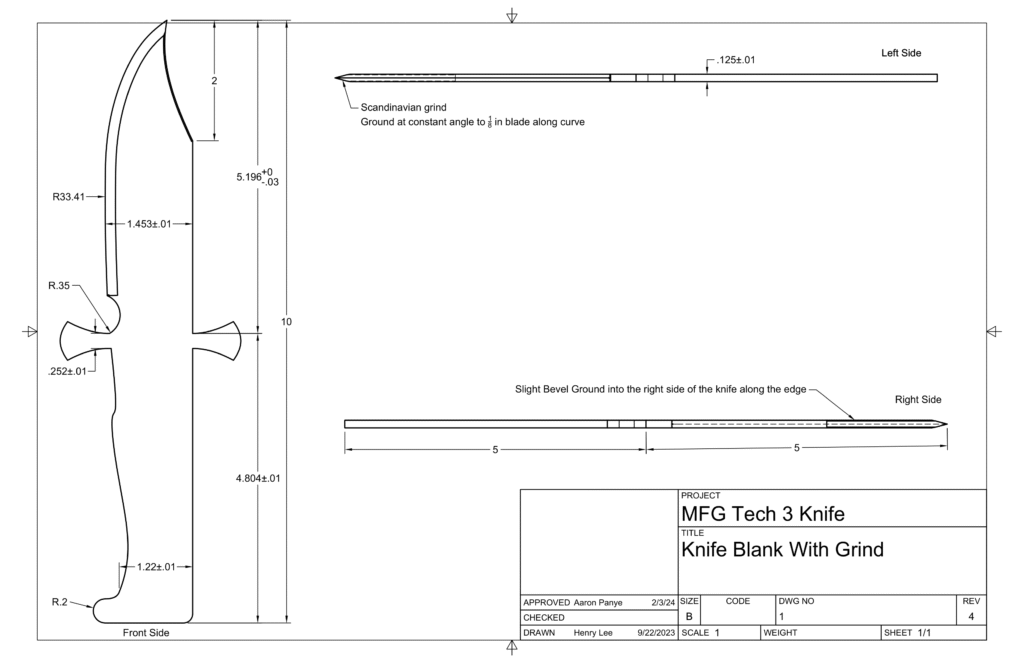
After heat treat, a group of 4 students would rough grind the edge of the blade at approximately 1.5 degrees.
The handles and sheaths were both designed by myself and two other students in F360. They were CAMed in Fusion and ran on a Tormach 24r CNC router. Since the handle shape was not flat, only the roughing of the profile was made with ball end mills. Sheaths were ran one at a time on SMW Mod Vices giving low setup times. Another couple students would then glue up the two halves of the sheath and finish sand them to 220 grit. Finally, the handle and sheaths were treated with mineral oil and the blade was polished.
This production project was the first time I had designed and seen the end of a mid-sized production run similar to what would be used during product verification and micro production runs. From this, I learned to design for manufacturability, manage multiple subteams, and it invigorated me to continue making more projects.